When SMART Local 5 (East Tennessee and North Carolina) member Steven Ruger became an organizer in April 2023, the local had around 1,100 members — the majority in Tennessee — with 500 sheet metal workers needed to take on several approaching megaprojects.
“I wanted to become an organizer to help build and grow Local 5,” said Ruger, who first joined the trade in July 2011 with SMART Local 112 (Elmira, N.Y.) before moving to North Carolina years later. “To give others the opportunity I had and build solidarity in North Carolina.”
By all conventional measures, he’s succeeding. Today, thanks in large part to aggressive organizing conducted by Local 5 and spearheaded by Ruger, the local has more than 1,500 members, and the size of Local 5’s North Carolina membership has increased by more than 60%.
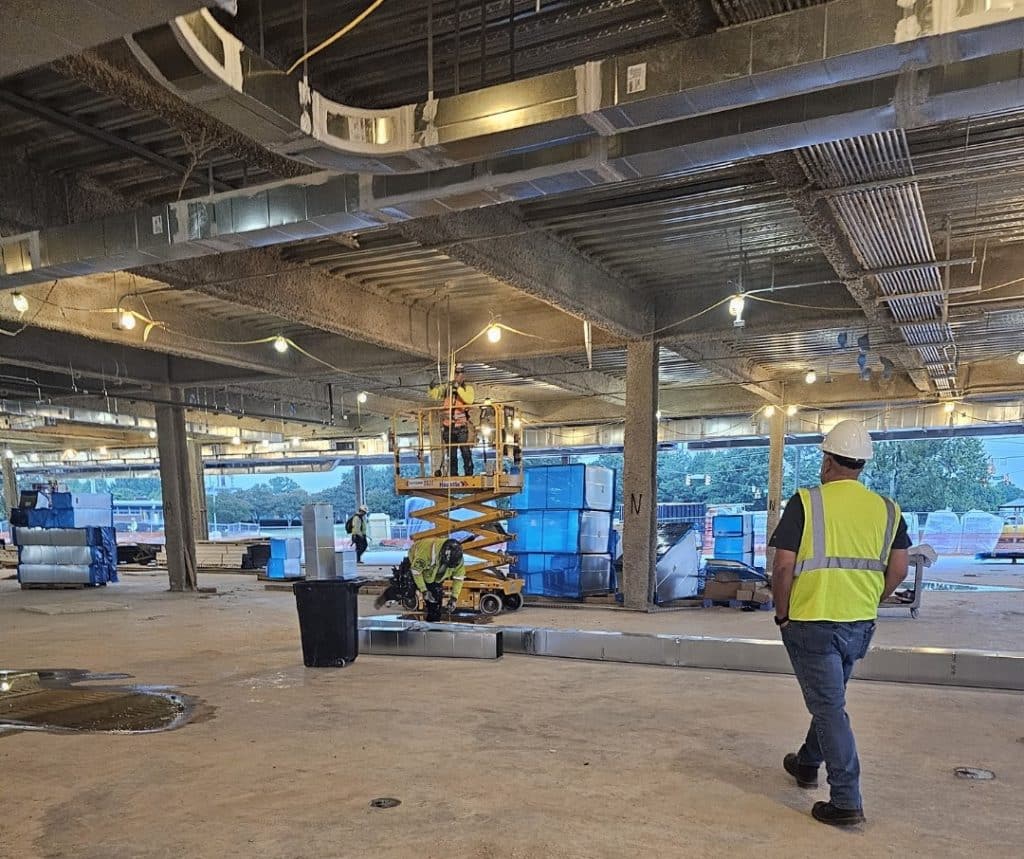
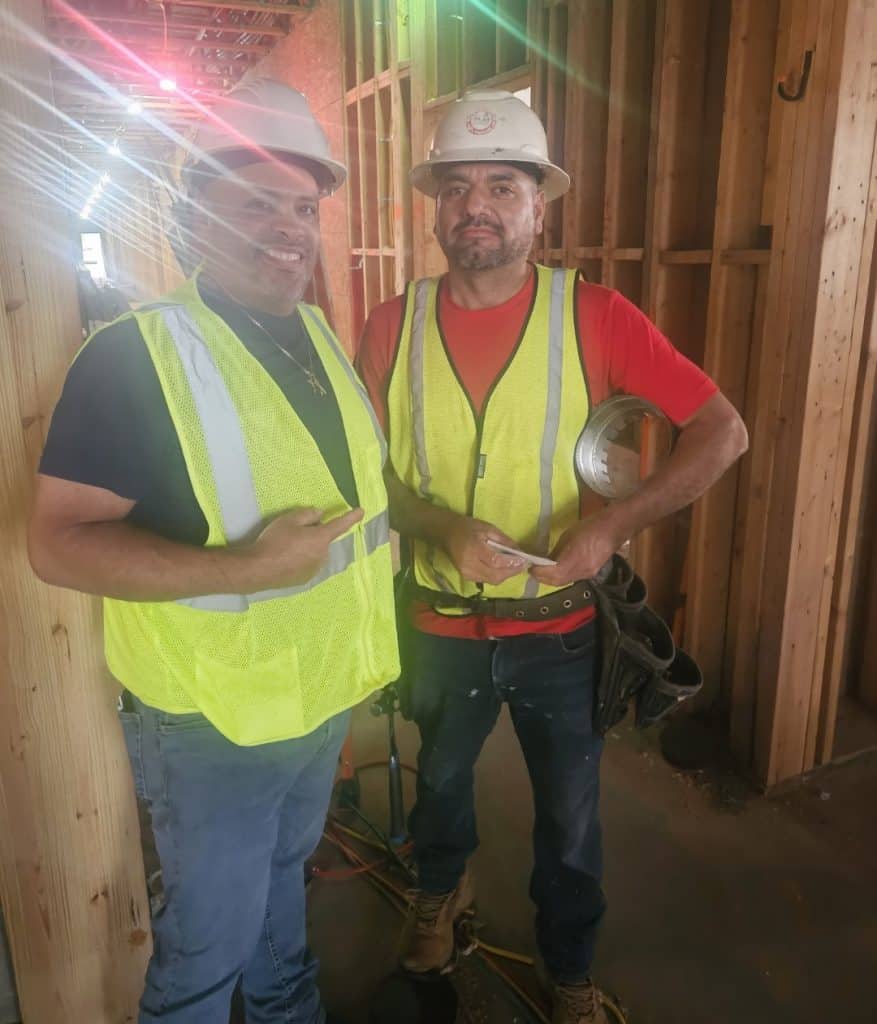
Megaprojects drive growth
Back in 2023, three megaprojects in Local 5’s jurisdiction — a Wolfspeed chip plant, a Toyota battery plant and a VinFast plant — put huge workforce demands on signatory contractors. That meant Ruger had to get straight to work once he started his new job as an organizer, training with now-retired International Organizer Kevin Mulcahy while simultaneously building a person-of-interest list for the local.
“Kevin and I researched nonunion fabrication shops in Charlotte, Raleigh and Greensboro, found where workers left these shops and placed yard signs at high-traffic intersections,” Ruger recalled.
In September 2023, the International put on an organizing blitz in Raleigh, North Carolina, to help staff the megaprojects, with organizers undergoing two days of training and two days of jobsite visits. There were four cars, with four organizers in each car, Ruger said — including one bilingual organizer per vehicle. He also had more than 500 palm cards printed, made up with a QR code that would direct users to a Local 5 landing page that explained megaprojects, pay scale, per diem, overtime and other facts about the union advantage.
“We flooded jobsites, gas stations and supply houses with these cards,” Ruger said. “This was a huge success.”
The recruiting didn’t stop there. Ruger ran ads on Craigslist and Indeed, marketing the many perks of being a Local 5 sheet metal worker. The local has partnered with Guilford Technical Community College to help bring on two classes of 25 first-year sheet metal apprentices. And Ruger found great success stripping one of Local 5’s nonunion competitors, Environmental Air Systems.
“On a couple jobs, I stripped the foreman, and he brought his whole crew of 10-plus people with him,” he said.
Language isn’t a barrier to the union advantage
Ruger, Mulcahy and Local 5 knew that navigating potential Spanish-English language barriers would be key to any organizing success in the area. Along with the bilingual organizers brought in for the Raleigh blitz, Ruger worked with International Organizer Josh Garner and Strategic Research and Data Team Manager Kris Harmon to make sure the Local 5 landing page could be translated into Spanish. He even invested in translator ear buds in order to communicate with Spanish-speaking workers directly.
“I would meet these workers at Sheetz gas stations and our local union hall, explaining all the benefits of joining,” Ruger said. “I hired a few bilingual workers, and going forward they would help me relay information and assist with recruiting.”
Bad-faith employers often exploit language barriers to keep workers from organizing, collectively bargaining and speaking up about jobsite issues. That wasn’t the case at SMART signatory contractor Dynamic Systems, Inc. (DSI), which took on the Wolfspeed chip plant in Siler City, North Carolina. Thanks to their cooperation, all workers were put in a position to succeed — benefiting the employer as well.
“DSI worked with Local 5 and set up two orientations for workers, one in English and one in Spanish,” Ruger explained. “I would send all Spanish-speaking workers to the shop on Friday, and then DSI would report them to the jobsite for orientation in Spanish.”
The success achieved by Ruger and Local 5 marks a roadmap for SMART locals across North America. A wide variety of challenges lie ahead for our organization, from workforce demands to encroaching nonunion competition. But regardless of the nation, state or municipality of any given local, there’s at least one action we can always take: organize, organize, organize.