SMART partners with SMACNA, ITI to highlight skilled trades as gateway to prosperous, in-demand careers
To raise awareness for the abundance and evolution of trade careers, building trades unions and skilled trade associations, including SMART, the Sheet Metal and Air Conditioning Contractors’ National Association (SMACNA) and International Training Institute (ITI), have come together to launch the first national Careers In Trades Week, April 7-11, 2025. Activities throughout the week will increase awareness about the benefits of choosing careers in the skilled trades among job seekers and the American public, with the goal of filling thousands of positions that are essential to the country’s economic growth.
“Union apprenticeships aren’t just a career path — they’re a gateway to a stable, rewarding future,” said SMART General President Michael Coleman. “By investing in the next generation of trade workers, we’re building a skilled workforce that will power our industries and communities for decades to come.”
“Skilled professions play critical roles in building the world in which we live, work, and play — vital to the construction of chip plants, stadiums, healthcare facilities, factories, and data centers. It’s time that we provide a fresh look at how trade careers have evolved technologically and financially,” added SMACNA CEO Aaron Hilger. “With approximately 35,000 sheet metal workers due to retire, the time to raise awareness of the opportunities and benefits among young workers is now.”
Stellar pay. In-demand work. No college debt.
Gen Z has been called the “toolbelt generation” due to their growing interest in joining the trades. It’s understandable considering the trades pay well, eliminate college debt and meaningfully contribute to society. According to a recent survey that was published in Higher Ed Dive, about 9 in 10 Gen Z graduates said learning a skilled trade can be a better route to economic security than college (Thumbtack survey).
It’s worth it. BLS occupational outlook predicts about 663,000 construction job openings each year. The same statistics showed a median annual wage of $55,000 in 2023, higher than that of all occupations. Furthermore, the Department of Labor’s Registered Apprenticeship Program provides training and education for hundreds of thousands of workers in fields ranging from construction to manufacturing to public administration. Within the sheet metal industry, training and working with union contractors can offer even greater rewards, with apprentices earning up to $87,500 in their first year and as much as $120,000 to $200,000 in wages and benefits within four to five years of completing an apprenticeship program.
Plus: High school students opting for a technical education career track can avoid college debt, which currently averages $34,000 for a four-year bachelor’s degree. Instead, students can get paid for apprenticeships and enter the workforce with money in the bank and no college debt.
“A 23-year-old on track to make six figures this year says he’s living proof that college isn’t necessary”
Read Fortune‘s profile of Local 265 sheet metal worker Tyler Zitzka
The work is rewarding, too. Working alongside other trades, union sheet metal workers are responsible for constructing, maintaining and repairing homes, schools, hospitals, buildings and other vital structures we use every day, ensuring the quality of the air we breathe. The skilled trade professions work together to construct the buildings that are essential to fueling the economy, including chip factories, data centers, state-of-the-art healthcare facilities and nuclear power plants.
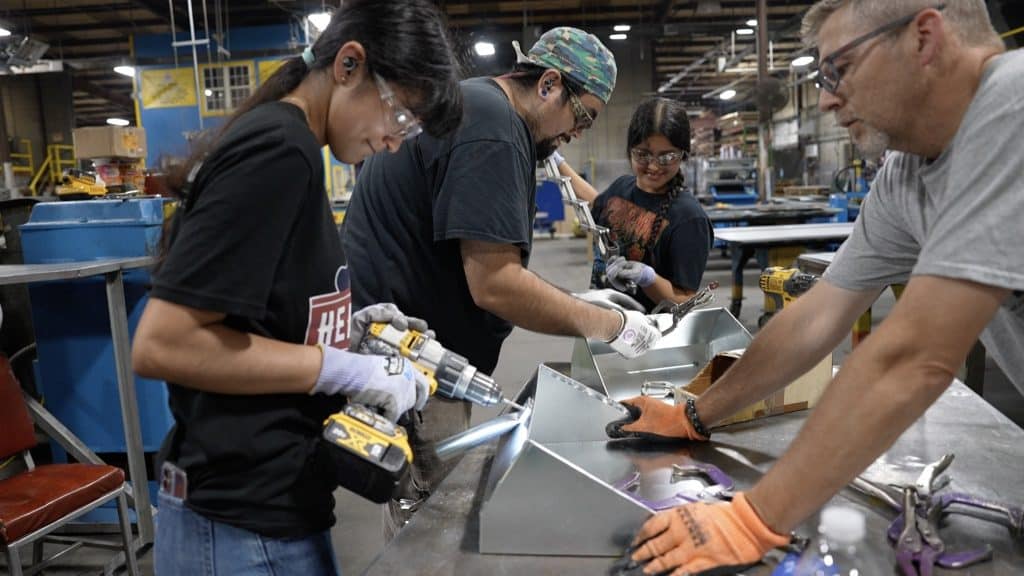
Interested in joining the unionized sheet metal trade? Find a training center near you.
Parents see the difference: Backed by strong bipartisan support, career and technical education programs are flourishing, and careers in the trades are projected to experience faster-than-average job growth from 2023 to 2033. They also offer earning potential that exceeds the median wage across all occupations, according to the BLS.
These reasons — along with the job market, economy, and college debt — may be why 89% of parents with children currently enrolled in high school or college think it’s smart for young adults to consider pursuing a career in the trades, according to new research conducted independently by Wakefield Research. The same research revealed that 48% of kids have mentioned wanting to go into a trade, and 86% of those parents would be open to or encourage it.