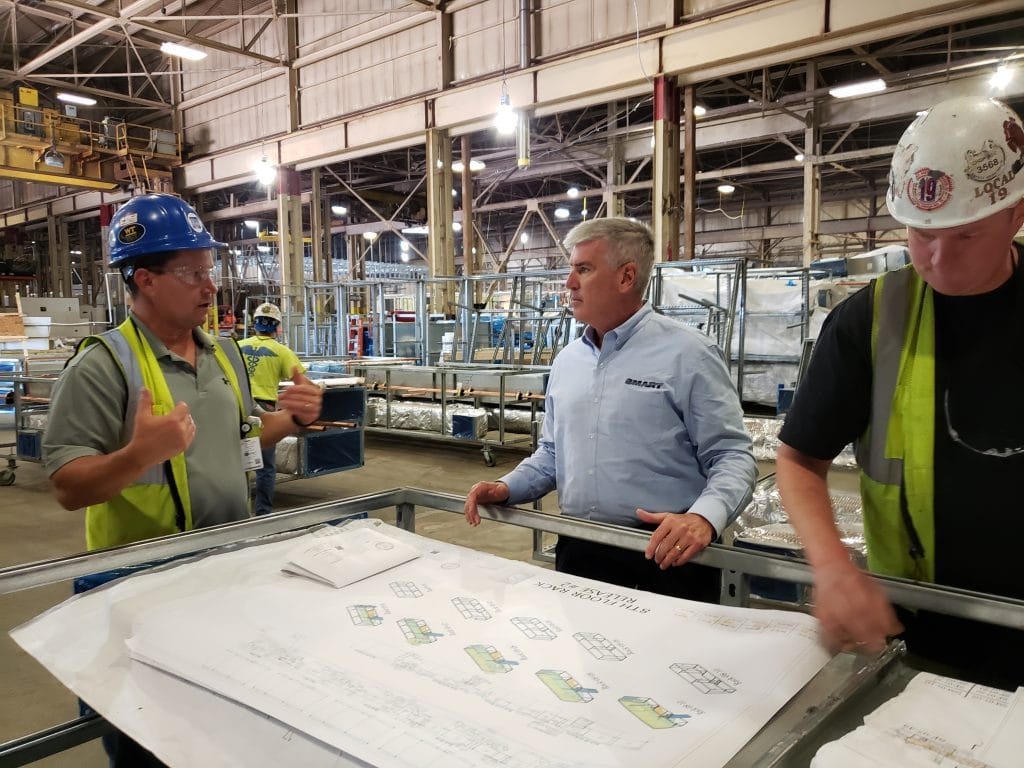
By: Todd Farally
On June 4th, SMART General President Joseph Sellers and Assistant to the General President Joseph Powell visited Local 19 members working at the Penn First rack building facility and Wm. J. Donovan’s thermaduct shop in Philadelphia, Pennsylvania. Both men wanted to witness SMART sheet metal workers doing what they do best—fabricate the highest-quality HVAC products anywhere and hear directly from members about their concerns and ideas regarding the state of the Union.
The first stop was the rack assembly facility that Local 19 signatory contractor Southland has set up in West Philadelphia. GP Sellers and Powell toured the facility along with Local 19 President Gary Masino and Assistant Business Manager Jerry Gontz. The shop is housed in what used to be a massive steel plant with plenty of room for all the trades to work. SSM Industries is on site with 10 members working to assemble the duct components in the racks.
Brother Ed Sparks, the Local 19 steward on site, explained how the installation process worked much like an assembly line to maximize efficiency and quality. The racks in question are mechanical rack systems that range in size from 11 feet by 5 feet to 18 feet by 8 feet. Each trade assembles and places components in the racks in a specific position as per the jobsite prints. The wheeled racks get rolled between the different sections of the shop. The sheet metal workers assemble the duct that is specific to each rack, then the insulator wraps the duct that is then it is placed in the rack. After that, the rack is rolled over to one of two fitting companies on site and the fitter adds their pipe, as does the plumber. After the top is welded on to the rack, it is held in storage until needed in the field.
When the racks are sent out to the field, they are loaded onto trucks with the wheels still attached, then transported to the Penn First Jobsite and craned up to the floor where they are to be installed. When reaching the floor, they are rolled into place, raised into position and hung where all the mechanical components line up with the components in the previous rack within the ceiling space. All that is left is to connect the two racks with a filler piece and the rest of the pieces that tie into the system. After the racks are hung, the wheels are removed and sent back to the shop to restart the process. Brother Farrell mentioned that this method of construction has been very beneficial out in the field. Not only does it facilitate a quick install, it also takes much of the staging materials onsite out of the equation. Penn First is the first project in Local 19’s territory to utilize this racking method and it has been very successful so far on the Penn First Project.
Next, the group headed over to Wm. J. Donovan for a short discussion and presentation of how Thermaduct is fabricated and how it will benefit our industry into the future. Shear Facts had a previous article on the new exterior duct product in 2018. Since that article, Wm. J. Donovan has fabricated numerous Thermaduct systems for other signatory contractors and have even installed a few itself. A group of Wm. J. Donovan’s upper management along with shop Foreman Mike DelGiorno and shop Steward Fred Stock met with SMART officials and walked them through the process of fabricating, the many benefits to the product including that the systems (when installed properly) are water tight, will last through all the elements and are a third of the weight compared to traditional exterior double-walled duct systems.
After the brief introduction to the product, the group headed to the fabrication shop across the street. When walking through the door it looks like any other fab shop, with material organized and stacked. But farther into the space, you start to notice this shop isn’t like many others in our trade. Straight duct and fittings are there throughout, but they’re a bit different than what most sheet metal workers are accustomed to with a poly-vinyl coating on the outside and what looks to be foil on the inside. Toward the back wall, you’ll see what looks like a plasma table with a long tube running from the mechanical arm to a canister. Over to the left there seems to be what resembles a brake. So as far as equipment is concerned, this shop doesn’t need much to function.
Local 19 members Brandon Steigerwald and Matt Watkins were on hand to give a tour on how Thermaduct is produced. Directly next to the table where the sheets are cut out there is a stack of Thermaduct sheets. On closer inspection, one can see that the sheets are essentially solid core insulation (similar to roof insulation) with a polyvinyl side while the other side has a foil material. Steigerwald and Watkins take a sheet over to the table, set the coordinates and let the machine do its work. The arm moves around and begins to route lines into the material on the foil side and then proceeds to cut an outline around the entire half section. After the machine finishes the process, Steigerwald takes the piece over to what is known as a thermal brake, which is used for bending the pieces just cut by heating up to anywhere between 325 and 375 degrees (depending on the surrounding temperature) and melting the vinyl coating on the material to where it is pliable enough to bend the piece into place.
After the sections are bended on the thermal brake, they are connected on each end, a flange product is affixed, stiffening rods added (as needed) and all seams are caulked. When installing in the field, an added layer of vinyl is added to surround where the connections are to ensure the product is completely water tight.
There are also added benefits to Thermaduct over traditional exterior systems aside from the weight and waterproof features. Because how it is constructed there is little to no deflection when the system becomes live. This means the duct isn’t moving or shifting as it would with a traditional system. This is a benefit because typically when there is defection, that movement of the duct (in or out) may loosen the insulation on the inside, with a possibility of the insulation finding its way into the airsteam.
The Thermaduct system is self-contained where deflection isn’t an issue, and these systems can withstand pressures of 10 in (plus or minus) water gauge. Wm. J. Donovan is a licensed fabricator of Thermaduct systems, serving Pennsylvania (east of Pittsburgh), South Jersey, parts of North Jersey, Delaware and the tip of Maryland.
The future possibilities for the next generation of sheet metal workers is seemingly endless with constant new technologies emerging every year. Our members will be there at the forefront of every innovation, ready to learn every new method and skill needed to continue to be the most knowledgeable, safe and valuable workers in the construction industry.
Related News
- Chairman Pauli Announces Retirement, SMART-TD celebrates his career
- SMART statement on Supreme Court’s decision regarding Kilmar Armando Abrego Garcia’s return to the United States
- SMART-TD Stands With Brother Kilmar Abrego Garcia
- New Mexico Local 1687 sets new precedent with Red Apple Transit
- Tentative Agreement Reached With TransitAmerica Services (TASI)
- SMART issues Monday, April 7, statement on Kilmar Armando Abrego Garcia’s ongoing case
- Local 5 organizes enormous growth in North Carolina
- Make sure your voice is heard, update your contact information
- SMART statement on Kilmar Armando Abrego Garcia’s right to due process
- Union leaders, community supporters to rally Friday, April 4, in support of Kilmar Armando Abrego Garcia and family